Continuus-Properzi has made major contributions in reducing the carbon emissions in the copper value chain with recycled and green copper through the Properzi Refining Technology.
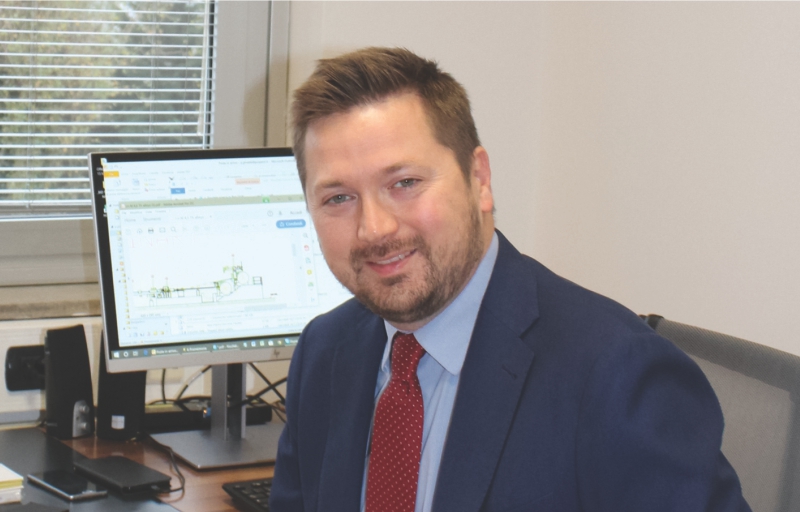
Copper (Cu), with its unique properties, is central to economic growth, quality of life, and sustainability. However, the base-metal producing sector, as well as the downstream processes, is under growing public pressure with respect to energy and water requirements and needs to meet several challenges, including increased demand and lower ore grades, and increased demand for electrical energy which generally requires greater use of resources.
In this article, we will emphasise and illustrate Continuus-Properzi’s significant contribution to reducing the CO2 emission in the Copper Chain with recycled and green copper through the Properzi Refining Technology, detailed in the following paragraphs, and the production of the Cu Green Wire through Properzi’s disruptive SAM (Self Annealing Microrolling®) technology.
A) Properzi Cu Refining Technology: Savings Up to 7’000 Kg CO2-eq per ton of FRHC Copper Rod Products Processing 100 percent Copper Scrap
The future challenges of the sector, in order to maintain its competitiveness, minimise carbon and water footprint, and achieve sustainable growth, include aspects related to exploitation and access of new resources, trade, research, and innovation activities, and the reduction of energy and water requirements.
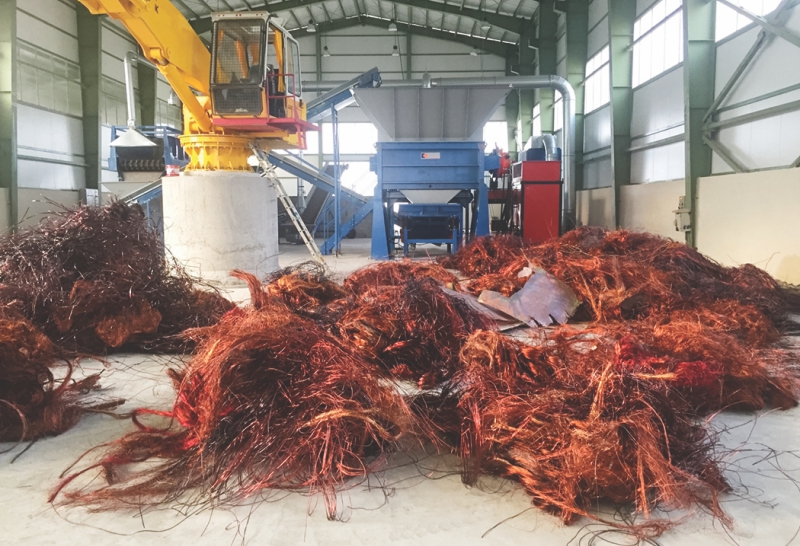
The decreasing ore grades result in environmental concerns such as a large waste/metal ratio and higher use of resources with respect to the use of energy, explosives, and water. The metal-producing sector is, on one hand, under growing public pressure, while on another hand, it needs to overcome several burdens such as, for example, increased demand for metals and the treatment of lower ore grades.
The most reputable publications on the Carbon Footprint of Cu production from primary sources calculate values of CO2 equivalent to producing 1 ton of Cu up to 8.5 t CO2-eq/t Cu in certain geographical regions, according to the required metallurgical production process. This value is consistent with what was retrieved from the various literature sources.
Copper can be 100 percent recovered from the majority of its end-products and returned to the production process without loss of quality during recycling. The production of secondary Cu is based on the direct melt of “new scrap” (waste resulting from either metal discarded in semis fabrication or generated during the initial manufacturing process) and/or the recycling of “old scrap” (obsolete end-of-life products or structures). Old scrap is often contaminated to a certain degree, depending mainly on its origin and the efficiency of its collection systems. Scrap metal recycling involves a number of steps such as recovery, sorting, brokering, baling, shearing, and smelting.
In the following paragraphs, we will provide more information on the types of copper scrap that can be refined thanks to the Properzi Refining Know-How and the wide range of furnaces and performances we can achieve. Here we focus our attention only on the reduction of the CO2-eq made possible with our technology in obtaining refined secondary Cu that is internationally identified as FRHC (Fire Refined High Conductivity).
The main processes used for obtaining secondary Cu are disassembly, sorting (according to different levels of purity), transportation, chopping, melting, and refining to remove the necessary quantities of impurities to reach the desired characteristics. The Properzi Refining Technology allows for to melt and refine selected Cu scrap (old, new or a mix of them) with a production ranging from 0.2 to 0.3 t CO2-eq/t Cu. According to the available literature, the average values for the upstream processes, mainly for Cu scrap transportation/preparation, vary from 0.25 to 0.35t CO2-eq/t Cu. The data indicates that the variation depends on the quality of the source material, the metallurgical process used and the quality of copper scrap.
According to our studies, we obtained results similar to the ones published by Giurco and Petrie in their work titled “Strategies for reducing the carbon footprint of copper: New technologies, more recycling or demand management?” issued by Minerals Engineering. We calculated that the Carbon Footprint to obtain 1 t of Cu from an ore (0.45 percent Cu) can reach 7.65 t CO2-eq; however, when Cu was obtained from a mix of 25 percent of 1st quality scrap (>99 percent Cu), 37.5 percent of 2nd quality scrap (>96 percent Cu), and 37.5 percent of low-quality scrap (>94 percent Cu) the Carbon Footprint was estimated to be reduced to 0.65t CO2-eq.
According to this data the production of FRHC Cu products from secondary Cu, that can replace with almost identical characteristics Cu products starting from primary Cu, thanks to the Properzi refining technology, can reduce the Carbon Footprint by as much as 7’000 Kg CO2-eq per ton of FRHC copper rod products processing 100 percent copper scrap (old and/or new).
Watch: Cable & Wire Fair Show Reel
B) Cu Green Wire: savings up to 50 percent of electrical energy per ton of 1.8-2.6mm wire starting from 8mm rod
In addition to the Refining Process, it is important to mention our revolutionary Self Annealing Microrolling technology that facilitates 50 percent energy savings. Even if the value of CO2-eq per ton is much lower compared to the one indicated for the refining process, its amount is important considering the millions of tons of copper rods processed into wire.
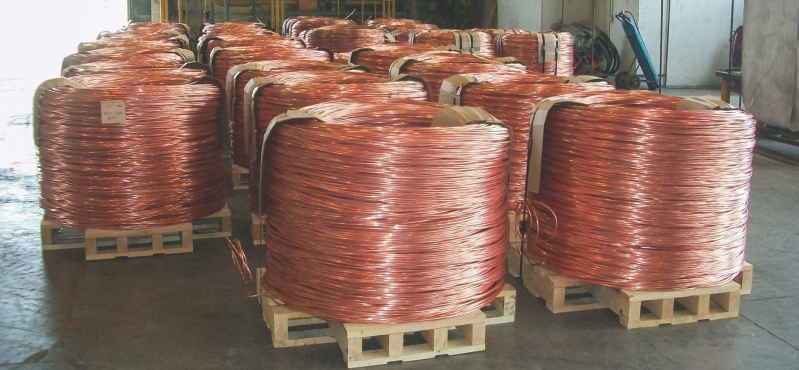
The production of Cu wire from 8 mm ETP rod has occurred for almost 50 years through the traditional breakdown drawing machines equipped with an inline electric annealer. During this period of time, the breakdown drawing machines have been subjected to several improvements both in mechanics and automation. However, the basic concept design still requires that the wire under process is cooled in each capstan before passing through the various dies so that the wire can then be subsequently heated and quenched by the annealing process in order to obtain soft wire. The fundamental limitations, strictly from the environmental point of view, of this consolidated process, can be summarised by saying a high consumption of electric energy, in the range of 90-110 kWh/t, is necessary for the recrystallization of the Cu wire through the annealer.
With the aim of resolving the problems listed above, Continuus-Properzi has designed, patented, manufactured, and tested a revolutionary system based on the well-proven Microrolling® mill as described here forth in the following paragraphs.
The concept design of Properzi’s new Process is based on the use of the rolling power to increase the temperature of the wire while being rolled so that it exits at a temperature which is above the recrystallization temperature. The costly power usage for the re-heating in the annealer is totally avoided. Furthermore, the electric power requested for the rolling operations at such temperature needs considerably less power compared with the power needed by a breakdown drawing machine.
This Properzi SAM Cu Microrolling® system is a revolutionary piece of equipment and, among all the other advantages that we will be glad to explain to you, is environmentally friendly with energy savings compared to traditional rod-breakdown operations of up to 50 percent (in the range of 90-110 kWh/t) while creating virtually no copper dust during the process. These two characteristics allow a savings of CO2-eq and, considering the millions of tons of copper rod processed in the traditional breakdown machine, the potential reduction of installed power plants of hundreds of Giga Watt.
Also Read: Continuus-Properzi: Eyeing India to Set Up Production Line
Conclusion
If you have the chance to visit our headquarters, we are sure that you will immediately understand Continuus-Properzi’s commitment to be not only an inventor of new technologies that have changed the traditional industrial practices in the Non-Ferrous sector but also our strong commitment to the environment and sustainability that is an integral part of our Company. This is evident at our headquarters with 20,000 square meters of greenery and hundreds of trees which existed when the company relocated to its current location; now these same trees are more than 70 years old.
The nature of our Company is to increase the efficiency of our equipment, reduce the consumption of utilities, and reduce waste by inventing new technological solutions for recycling copper scrap. As explained above it is possible to convert 100 percent low-quality copper scrap directly into a high-quality copper rod. We have spent tremendous effort in the realisation of these goals and we continue to work to improve upon the significant results already reached. We summarised these results here below:
A. Properzi Cu Refining Technology: savings up to 7’000 Kg CO2-eq per ton of FRHC copper rod products processing 100 percent copper scrap.
B. Cu Green Wire: savings up to 50 percent of electrical energy per ton of 1.8-2.6mm wire produced starting from 8mm rod.
The goal of the global community is to make the Copper Chain “greener” and Continuus-Properzi continues to make a significant contribution in this field.